Como o Inversor de Frequência Motor Transforma o Desempenho de Máquinas
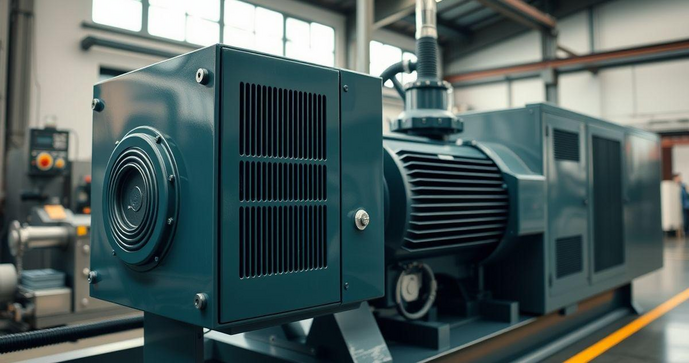
Por: Ângelo - 25 de Abril de 2025
Princípios Básicos do Inversor de Frequência
O inversor de frequência é um dispositivo eletrônico que controla a velocidade e o torque de motores elétricos, especialmente os motores de indução. Ele consegue isso ajustando a frequência e a tensão da alimentação elétrica fornecida ao motor. Ao variar a frequência, o inversor permite que o motor opere em diferentes velocidades, adaptando-se às necessidades específicas de cada aplicação.
Os princípios básicos do funcionamento de um inversor de frequência envolvem a conversão da corrente elétrica. Normalmente, a rede elétrica fornece corrente alternada (CA), mas o inversor transforma essa corrente em corrente contínua (CC) por meio da retificação. Esta CC é então convertida novamente em CA com a frequência e a tensão desejadas, utilizando um processo chamado inversão.
Este processo de conversão é realizado por meio de componentes eletrônicos, como transistores e diodos, que desempenham um papel fundamental na eficiência e no controle preciso da alimentação do motor. Além disso, os inversores modernos frequentemente incorporam tecnologia digital, permitindo configurações e monitoramento remoto, o que aumenta ainda mais sua versatilidade.
A capacidade do inversor de alterar a frequência da corrente elétrica é o que possibilita a regulação da velocidade do motor, desde baixas rotações até velocidades máximas. Essa flexibilidade é especialmente útil em aplicações industriais, como em esteiras transportadoras, ventiladores e bombas, onde a demanda de carga pode variar significativamente.
Em resumo, os princípios básicos do inversor de frequência são fundamentais para entender como esses dispositivos podem otimizar o desempenho dos motores elétricos, possibilitando não apenas a variação de velocidade, mas também a economia de energia e a redução do desgaste mecânico dos equipamentos.
Vantagens do uso de Inversores em Motores Elétricos
A utilização de inversores de frequência em motores elétricos oferece uma série de vantagens significativas que melhoram o desempenho geral dos equipamentos. Uma das principais vantagens é a eficiência energética. Os inversores permitem que os motores operem apenas na velocidade necessária para realizar uma tarefa específica, reduzindo assim o consumo de energia em comparação com sistemas que operam em velocidade constante.
Outra vantagem importante é o controle preciso da velocidade e do torque do motor. Isso se traduz em maior flexibilidade operacional, permitindo ajustes rápidos em processos industriais. Por exemplo, em aplicações de bombas e compressores, o uso de inversores pode ajudar a otimizar a operação, ajustando a velocidade de acordo com a demanda real, o que pode resultar em economia significativa.
Além disso, a implementação de inversores pode aumentar a vida útil dos motores. A capacidade de iniciar e parar o motor gradualmente, em vez de fazê-lo abruptamente, reduz a tensão mecânica sobre os componentes, prevenindo desgastes prematuros e minimizando a necessidade de manutenção frequente.
Os inversores também são conhecidos por oferecerem funções avançadas de proteção ao motor, como sobrecarga e sobretemperatura. Isso significa que, em caso de falhas ou condições adversas, o inversor pode desativar automaticamente o motor, evitando danos e aumentando a segurança da operação.
A possibilidade de monitoramento e controle remoto é outra vantagem que não pode ser subestimada. Muitos inversores modernos possuem conectividade com sistemas de automação industrial, permitindo que os operadores acompanhem o desempenho do motor em tempo real e façam ajustes conforme necessário, aumentando a produtividade e a eficiência operacional.
Como Funciona um Inversor de Frequência na Prática
O funcionamento de um inversor de frequência na prática se dá em diversas etapas que garantem o controle preciso da velocidade do motor. Inicialmente, o inversor recebe a tensão da rede elétrica e, através de um processo de retificação, converte a corrente alternada (CA) em corrente contínua (CC). Isso é feito por meio de diodos que permitem a passagem da corrente em uma única direção.
Após a retificação, a corrente contínua é filtrada para suavizar qualquer ondulação residual, tornando-a mais estável para o próximo estágio. Em seguida, essa energia CC é invertida novamente para corrente alternada com a frequência desejada. Este processo é realizado utilizando transistores de potência, que operam em alta velocidade e permitem uma modulação da largura de pulso (PWM).
A modulação da largura de pulso é fundamental, pois controla a tensão e a frequência enviadas ao motor. Quanto maior a frequência, maior será a velocidade do motor, enquanto a diminuição da frequência resultará em uma redução da velocidade. A capacidade de alterar essas variáveis em tempo real permite um funcionamento eficiente e adaptável do motor, conforme as necessidades da aplicação.
Durante o funcionamento, o inversor também monitora parâmetros como corrente, tensão e temperatura do motor. Com isso, ele pode realizar ajustes automáticos para otimizar o desempenho e garantir a segurança. Por exemplo, se o motor começar a superaquecer, o inversor pode diminuir a velocidade ou interromper a operação para evitar danos.
Além disso, muitos inversores vêm equipados com funções de programação que permitem definir perfis de operação específicos para diferentes condições de carga. Isso significa que, dependendo da aplicação, o inversor pode ser programado para operar em modos distintos, maximizando a eficiência e a eficácia do motor em variados cenários.
Aplicações Comuns de Inversores de Frequência em Indústrias
Os inversores de frequência são amplamente utilizados em diversas aplicações industriais devido à sua versatilidade e eficiência. Entre as aplicações mais comuns estão as bombas industriais, onde a capacidade de ajustar a velocidade de operação permite que a entrega de fluidos seja otimizada de acordo com a demanda, resultando em economia de energia e prolongamento da vida útil dos equipamentos.
Outro setor que se beneficia do uso de inversores de frequência é o de ventiladores e compressores. A regulação precisa da velocidade do motor pode melhorar a eficiência do fluxo de ar e da compressão de gases, ajustando-se de acordo com as necessidades do sistema. Isso é especialmente relevante em instalações de climatização, onde a eficiência energética é crítica.
Os transportadores também têm se tornado uma aplicação frequente para inversores de frequência. Com a integração desses dispositivos, é possível controlar a velocidade do transportador, garantindo um fluxo contínuo e eficiente de materiais, além de reduzir o consumo de energia em momentos de baixa demanda.
Além disso, os inversores são utilizados em equipamentos de processamento industrial, como misturadores e trituradores. O controle de velocidade e torque ajuda a otimizar os processos de mistura e moagem, assegurando uma qualidade de produto final consistente ao ajustar as operações com base nas características dos materiais processados.
Por fim, as máquinas-ferramenta também se beneficiam do uso de inversores de frequência. Em processos de usinagem, a variação da velocidade do motor pode ser fundamental para alcançar cortes precisos e eficientes em diferentes tipos de materiais, adaptando-se às exigências de cada operação.
Dicas para Escolher o Inversor de Frequência Ideal
Escolher o inversor de frequência ideal é uma decisão crucial que pode impactar diretamente a eficiência do seu sistema. Para isso, é fundamental considerar a potência do inversor, que deve ser compatível com a potência do motor que será utilizado. Um inversor subdimensionado pode levar a falhas de desempenho, enquanto um superdimensionado pode resultar em custos desnecessários.
Outro fator a ser considerado é a faixa de frequência e tensão que o inversor pode fornecer. Certifique-se de que o modelo escolhido atenda às necessidades específicas da sua aplicação. Por exemplo, se o motor demandar uma operação em altas frequências, escolha um inversor que suporte essa faixa sem comprometer o desempenho.
A eficiência do inversor também é um aspecto importante. Modelos que oferecem alta eficiência energética não só minimizam o consumo de energia, mas também reduzem a geração de calor, prolongando a vida útil do equipamento. É recomendável verificar as classificações de eficiência do produto antes da compra.
Além disso, a presença de recursos avançados, como controle remoto e programação, pode ser um diferencial significativo. Inversores que permitem configurações personalizadas facilitam o ajuste das operações conforme as necessidades das máquinas, conveniências que podem gerar grandes economias de tempo e custo.
Por fim, a reputação do fabricante e o suporte técnico disponível também são fatores que não devem ser negligenciados. Optar por marcas reconhecidas pode garantir acesso a assistência e manutenção, aumentando a confiabilidade do seu investimento a longo prazo.
Manutenção e Cuidados Necessários para Inversores de Frequência
A manutenção adequada dos inversores de frequência é essencial para garantir seu desempenho eficiente e prolongar sua vida útil. Um dos principais cuidados a serem tomados é a limpeza regular do equipamento. Poeira e sujeira podem acumular-se nos componentes eletrônicos, interferindo na operação e causando superaquecimento. É recomendável realizar uma inspeção visual e remover qualquer sujeira acumulada periodicamente.
Além da limpeza, a verificação das conexões elétricas é fundamental. Certifique-se de que todos os cabos e terminais estão bem conectados e em boas condições, pois conexões soltas ou danificadas podem levar a falhas operacionais. A monitorização da fiação ajuda a prevenir problemas maiores antes que se tornem críticos.
Outro aspecto a se considerar é o controle de temperatura. Os inversores de frequência devem operar dentro de uma faixa de temperatura adequada para garantir seu funcionamento ideal. Monitorar a temperatura ambiente e garantir boa ventilação ao redor do inversor pode prevenir danos térmicos e falhas.
Realizar testes de desempenho regulares é uma prática recomendada. Monitore a eficiência do inversor verificando a saída de frequência e tensão, assim como a resposta do motor. Se houver alterações inesperadas nos parâmetros de operação, isso pode indicar a necessidade de manutenção ou ajustes.
Por fim, consulte o manual do fabricante para seguir as recomendações de manutenção específicas para o seu modelo. O cumprimento dessas diretrizes pode incluir a substituição de componentes desgastados ou a atualização de software, garantindo que o inversor continue funcionando de maneira eficaz ao longo do tempo.
Em resumo, o inversor de frequência é um elemento crucial para otimizar o desempenho de motores elétricos em diversas aplicações industriais.
Compreender seus princípios de funcionamento, vantagens e as melhores maneiras de escolher e manter esse equipamento pode fazer uma grande diferença na eficiência e na economia de energia.
A manutenção regular e os cuidados adequados garantem a longevidade do inversor, contribuindo para operações mais seguras e confiáveis.
Ao investir em um inversor de frequência de qualidade e aplicar as práticas recomendadas, os usuários podem maximizar os benefícios e impulsionar a produtividade de suas operações.