Como o Inversor de Frequência para Motor Pode Transformar Sua Indústria
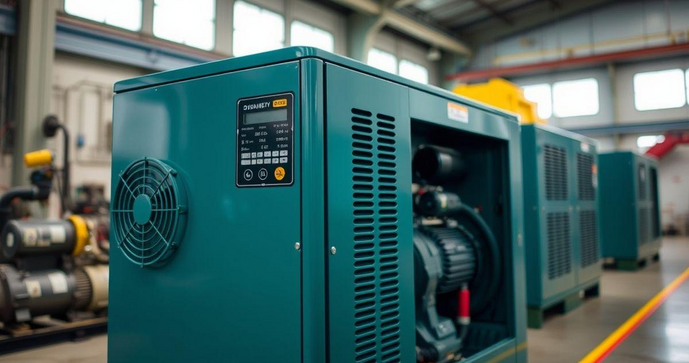
Por: Ângelo - 24 de Março de 2025
O que é um inversor de frequência e como funciona
Um inversor de frequência é um dispositivo eletrônico responsável pelo controle da velocidade e do torque de motores elétricos. Ele funciona alterando a frequência e a tensão da corrente elétrica que alimenta o motor, permitindo ajustar a sua velocidade conforme a necessidade do processo industrial.
A funcionalidade do inversor de frequência baseia-se na conversão de corrente alternada (CA) em corrente contínua (CC) e, em seguida, a reconversão dessa corrente em CA com a frequência desejada. O processo se inicia com a retificação da energia elétrica, onde a corrente alternada é convertida em contínua. Em seguida, um inversor recria a corrente alternada na frequência adequada para o motor, utilizando a técnica de modulação por largura de pulso (PWM), que garante um bom controle sobre o motor.
Essa tecnologia traz muitos benefícios, como a redução do consumo de energia, melhoria na eficiência operacional e melhor controle de processos, especialmente em aplicações que necessitam de variações de velocidade. Com um inversor de frequência, os motores não funcionam em máxima potência o tempo todo, mas sim em níveis otimizados, de acordo com as demandas do sistema.
Além disso, os inversores de frequência contribuem para a proteção do motor, evitando picos de corrente na partida e reduzindo o desgaste mecânico. Eles também permitem a configuração de limites de velocidade, direção, e modos de operação, oferecendo flexibilidade e segurança ao usuário.
Com a crescente demanda por eficiência energética e sustentabilidade nas indústrias, os inversores de frequência tornaram-se peças chave na automação industrial moderna, proporcionando soluções práticas e eficientes para o controle de motores elétricos.
Vantagens da utilização de inversores de frequência em motores
A utilização de inversores de frequência em motores oferece um conjunto significativo de vantagens que impactam diretamente na eficiência operacional e na redução de custos. Um dos principais benefícios é a economia de energia, pois esses dispositivos ajustam a velocidade do motor conforme a demanda do processo, evitando o desperdício de eletricidade.
Outra vantagem importante é a melhoria no controle de processos. Inversores de frequência permitem ajustes precisos na velocidade e no torque, possibilitando uma operação mais flexível e adaptável às necessidades específicas de cada aplicação. Isso é especialmente relevante em indústrias que requerem variações frequentes de velocidade.
A redução do desgaste mecânico é também um ponto positivo. Com o controle adequado da aceleração e desaceleração do motor, os inversores minimizam o estresse nos componentes mecânicos, prolongando a vida útil do equipamento. Com isso, são necessárias menos intervenções de manutenção e os custos operacionais são reduzidos.
Além disso, os inversores de frequência oferecem uma proteção eficaz para os motores. Eles evitam picos de corrente que podem danificar o motor durante a partida e oferecem funcionalidades como proteção contra sobrecarga e superaquecimento. Esses mecanismos de segurança aumentam a confiabilidade do sistema.
A automação e a integração com sistemas de controle também se tornam mais simples com o uso de inversores de frequência. Eles podem ser facilmente conectados a redes de automação industrial, permitindo um controle centralizado e a implementação de estratégias de otimização de processos, como a manutenção preditiva.
Em resumo, as vantagens da utilização de inversores de frequência incluem economia de energia, controle preciso dos processos, redução do desgaste e da necessidade de manutenção, proteção dos motores e facilitação da automação. Essas características tornam os inversores uma solução indispensável em aplicações industriais modernas.
Como escolher o inversor de frequência ideal para sua aplicação
Escolher o inversor de frequência ideal para sua aplicação é uma etapa crucial que pode influenciar diretamente o desempenho e a eficiência de seu sistema. O primeiro fator a considerar é a potência do motor. O inversor deve ser dimensionado para suportar a potência nominal do motor, garantindo que ele funcione de maneira segura e eficaz. Normalmente, os inversores são classificados em watts (W) ou quilowatts (kW).
Outro aspecto importante é a faixa de frequência de operação. É essencial que o inversor escolhido permita a variação de frequência necessária para sua aplicação específica. A faixa habitual varia, mas um inversor típico deve operar em uma frequência de pelo menos 0 a 60 Hz, podendo ser ajustado conforme as demandas dos processos.
A compatibilidade com o tipo de motor também deve ser verificada. Existem inversores específicos para motores de indução, motores síncronos e motores de corrente contínua. Certifique-se de que o equipamento escolhido é projetado para o tipo de motor que você possui, garantindo a sua eficiência e segurança.
Avaliar as funcionalidades adicionais do inversor também é fundamental. Muitos modelos oferecem características extras como controle de torque, programação de rampas de aceleração e desaceleração, e proteções integradas contra sobrecarga e superaquecimento. Funcionalidades como interfaces de comunicação para integração com sistemas de automação também são um ponto a considerar.
E por último, leve em conta a facilidade de instalação e a manutenção. Escolher um inversor que tenha um manual claro e suporte técnico acessível pode facilitar a implementação e o uso. Além disso, esteja atento aos custos não apenas de aquisição, mas também de operação e manutenção a longo prazo.
Em suma, a escolha do inversor de frequência ideal deve levar em consideração a potência do motor, a faixa de frequência, a compatibilidade com o tipo de motor, funcionalidades adicionais e a facilidade de instalação e manutenção. Esses fatores ajudam a garantir que o sistema opere de maneira eficiente e segura.
Instalação de inversores de frequência: o que você precisa saber
A instalação de inversores de frequência é um processo vital que deve ser realizado com atenção e cuidado para garantir o funcionamento adequado do sistema. O primeiro passo consiste em escolher um local apropriado para a instalação. O inversor deve ser montado em um ambiente limpo e seco, longe de fontes de calor excessivo, umidade e vibrações, garantindo sua durabilidade a longo prazo.
Antes de iniciar a instalação, é importante ter em mãos o manual do usuário e todas as ferramentas necessárias, como chaves de fenda, alicates e cabos apropriados. Certifique-se de que todos os dispositivos estão desconectados da fonte de energia e que a área de trabalho está segura.
O próximo passo é realizar a conexão elétrica. Isso inclui a ligação da fonte de alimentação ao inversor e posteriormente ao motor. As ligações devem ser feitas de acordo com as especificações do fabricante, respeitando a polaridade e garantindo que os cabos estejam firmemente conectados. É altamente recomendado que essa etapa seja realizada por um eletricista qualificado para evitar riscos elétricos e garantir uma instalação correta.
Além das conexões elétricas, a instalação dos sensores e dispositivos de segurança deve ser feita de forma cuidadosa. Os sensores de sobrecarga e temperatura, por exemplo, precisam estar posicionados de forma a monitorar efetivamente as condições de operação do motor. Esses dispositivos são essenciais para a proteção do sistema e devem ser testados para assegurar o correto funcionamento.
Uma vez que todas as conexões estão realizadas, o seguinte procedimento é a configuração do inversor. A configuração inicial deve ser feita seguindo as orientações do fabricante, que incluem selecionar a frequência nominal, ajustar rampas de aceleração e desaceleração, e programar proteções. Certifique-se de verificar todos os parâmetros e funcionalidades disponíveis para otimizar a operação do sistema.
Por fim, após concluir a instalação e configuração, é crucial realizar testes de funcionamento. Verifique se o motor opera corretamente em diferentes frequências e se os dispositivos de segurança respondem adequadamente. Documente o procedimento de instalação e torne-se familiarizado com o manual do usuário, para facilitar futuras manutenções.
Manutenção de inversores de frequência: dicas e cuidados
A manutenção adequada dos inversores de frequência é fundamental para garantir o desempenho eficiente e a durabilidade do equipamento. Um dos principais cuidados que devem ser tomados é a realização de limpezas regulares. Poeira, sujeira e resíduos podem acumular-se nos componentes do inversor, afetando seu funcionamento. Use um pano seco e limpo para limpar a carcaça e os dissipadores de calor, evitando o uso de líquidos que possam danificar componentes internos.
Além da limpeza, é importante verificar as conexões elétricas periodicamente. Certifique-se de que todos os cabos e terminais estão bem conectados e livres de corrosão. Conexões soltas podem gerar falhas no funcionamento e riscar danos aos componentes internos do inversor.
A monitorização das temperaturas de operação é outra medida de manutenção importante. Inversores de frequência podem gerar calor durante a operação, e temperaturas excessivas podem levar a falhas. Utilize sensores de temperatura e faça testes regulares para garantir que o inversor esteja funcionando dentro das temperaturas normais especificadas pelo fabricante.
Realizar atualizações de software e firmware do inversor também é um passo recomendado. Os fabricantes frequentemente disponibilizam atualizações que podem melhorar o desempenho, corrigir bugs e aumentar a eficiência. Mantenha-se informado sobre as atualizações disponíveis e aplique-as conforme necessário.
É aconselhável criar um cronograma de manutenção preventiva, incluindo inspeções e testes regulares. Durante essas avaliações, verifique o funcionamento geral do inversor e faça ajustes e reparos conforme necessário. Documentar qualquer manutenção realizada é uma prática útil para monitorar o histórico de cuidados com o equipamento.
Por fim, não hesite em consultar o suporte técnico do fabricante ou contratar um profissional qualificado para assistência sempre que necessário. Profissionais experientes podem detectar e resolver problemas que podem passar despercebidos, assegurando que o seu inversor de frequência opere de forma confiável e eficiente.
Principais aplicações de inversores de frequência na indústria
Os inversores de frequência desempenham um papel crucial em diversas aplicações industriais, contribuindo para a eficiência e automatização dos processos. Uma das aplicações mais comuns é no controle de motores de bombas. Ao ajustar a velocidade das bombas conforme a demanda de fluxo, os inversores ajudam a economizar energia e a reduzir o desgaste dos equipamentos.
Outra aplicação significativa é em sistemas de ventilação e climatização. Inversores de frequência são utilizados para regular a velocidade dos ventiladores e compressores, melhorando o controle da temperatura e da qualidade do ar, enquanto minimizam o consumo energético.
Na indústria de manufatura, esses dispositivos são amplamente utilizados em correias transportadoras e sistemas de transporte automático, permitindo que a velocidade de movimentação seja ajustada de acordo com o ritmo da linha de produção. Essa flexibilidade resulta em uma operação mais eficiente e melhor sincronização entre as etapas do processo produtivo.
Os inversores de frequência também são utilizados em prensa e maquinário industrial, onde a precisão e o controle de torque são essenciais. Eles permitem que os operadores ajustem dinamicamente a carga e a velocidade de operação, otimizando a produção e melhorando a qualidade dos produtos finais.
Além disso, na indústria de alimentos e bebidas, os inversores de frequência são usados para controlar misturadores, trituradores e equipamentos de embalagem. Com a capacidade de ajustar a velocidade, os operadores podem garantir que os ingredientes sejam processados de forma consistente e eficiente, elevando a qualidade do produto.
Em suma, as principais aplicações de inversores de frequência na indústria incluem o controle de motores de bombas, sistemas de ventilação, transportadores, maquinário de fabricação e processamento de alimentos. A versatilidade desses dispositivos os torna indispensáveis para a melhoria da eficiência energética e a automação de processos industriais.
Em resumo, a adoção de inversores de frequência nos sistemas industriais é um investimento que oferece inúmeras vantagens, como economia de energia, maior controle de processos e proteção dos motores.
A correta seleção, instalação e manutenção dos inversores são práticas essenciais que garantem um desempenho eficiente e prolongam a vida útil dos equipamentos.
Com suas diversas aplicações, que vão desde bombas e ventiladores até maquinário de fabricação, os inversores de frequência se tornam aliados indispensáveis na automação industrial moderna.
Portanto, apostar nessa tecnologia é viabilizar melhorias significativas e sustentáveis para a indústria.